Hohlkörpermodule für Geschossdecke
In unmittelbarer Nähe des Berliner Hauptbahnhofs und Regierungsviertels gelegen, entsteht nördlich des Berliner Stadtzentrums auf rd. 85000m2 ein neues Stadtquartier. Jetzt noch eine imposante Großbaustelle, wird es in wenigen Jahren eine moderne Stadt in der Stadt sein. Das „Quartier Heidestrasse“ bietet dann perfekte Bedingungen für Wohnen, Arbeiten und Leben auf engstem Raum. Ähnlich der Neubebauung des Potsdamer Platzes wurden auch hier unter- schiedliche renommierte Architekturbüros mit der Planung der Wohn- und Bürogebäude, öffentlichen Straßen und Plätzen sowie der Grünflächen beauftragt.
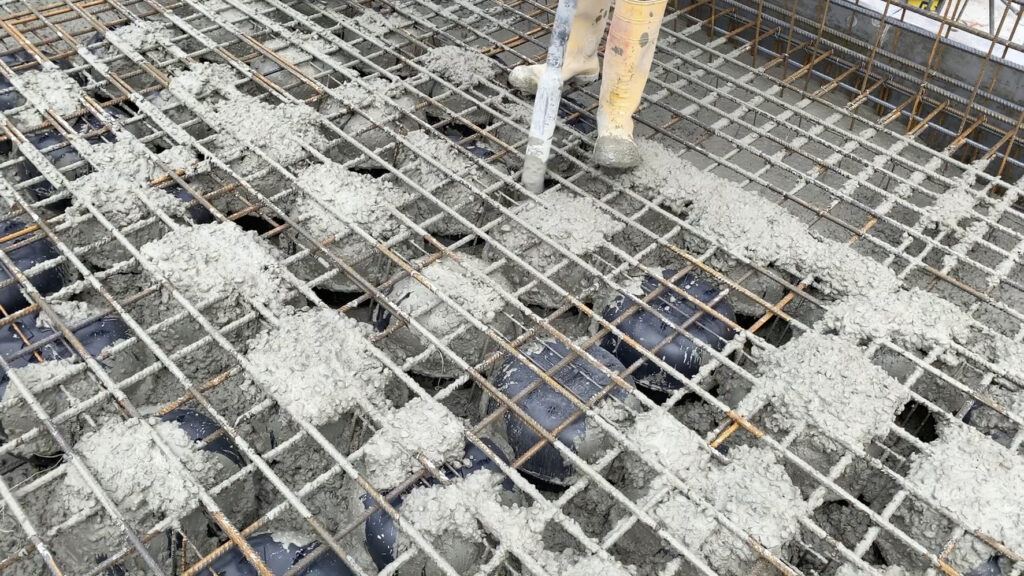
Lastreduzierung hat viele Vorteile
Das „QH Track“ steht kurz vor der Fertigstellung, ein langgezogener Gebäuderiegel mit einzelnen aufragenden Türmen, von denen aus man bis ins Regierungsviertel blicken kann. Das in Zürich und Berlin an- sässige Architekturbüro EM2N Architekten konzipierte mit dem QH Track einen modernen Büro- und Warehouse-Gebäude- komplex, mit Raumhöhen von teilweise bis zu vier Metern sowie weitgespannten Geschossdecken. Hohe Spannweiten erfordern üblicherweise viel Bewehrungsstahl sowie einen großen Deckenquerschnitt. Doch es geht auch anders: mit weniger Eigengewicht, also weniger Beton sowie Stahl. Die Berliner Niederlassung des Bauunternehmens Zech Hochbau AG erstellte bei diesem Projekt erstmals in enger Zusammenarbeit mit der Cobiax Deutschland GmbH die Decken in Hohlkörpertechnologie.
Reduktion auf das Notwendige
Besonders in Bürobauten sind weitgespannte Decken Standard, denn je nach Nutzung ergeben sich sehr unterschiedliche Strukturen – über Einzelbüros bis hin zu durchgehenden Bürolandschaften. Diese Konzepte unterlie- gen zudem einem ständigen Wandel. Um die erforderliche Biegesteifigkeit weit gespannter Decken zu erzielen, sind Dicken von bis zu 50 cm keine Seltenheit und es macht besonders in diesen Fällen wenig Sinn, über die gesamte Deckenlänge zu betonieren. Die statisch wirksamen Druck- und Zugzonen liegen in den Randbereichen, oben und unten, dort wo auch die Bewehrung eingelegt wird. Je nach Bewehrung und Deckenspannweite werden für Einbettung und Überdeckung der Armierungseisen maximal rd. 40 % der Deckendicke statisch genutzt. Die „Mitte“ übernimmt lediglich die Übertragung der Querkräfte. Diese sind vergleichsweise gering – bewehrte Betonstege könnten diese Lasten problemlos aufnehmen. Lediglich in Bereichen mit hoher Querkraft muss die Decke vollmassiv ausgeführt werden. Dies betrifft im Mittel 30 % der Gesamtdeckenfläche. Vereinfacht zusammengefasst: Nahezu 35 % des Betons im Hohlkörperbereich fungieren als hochwertiges Verfüllmaterial, das mit einem Eigengewicht von 2000 kg/m3 bis 2600kg/m3 die Deckenkonstruktion zusätzlich belastet und auch kräftig auf die Fundamente drückt. Beim QH Track mit einer Geschossdeckenfläche von über 100000m2 bedeutet dies, dass 8000m3 Beton statisch nicht wirksam verbaut werden – eine mittlere Deckenstärke von 32 cm vorausgesetzt. Rund 20000t Beton müssen transportiert und verarbeitet werden, 20 000 t eigentlich nicht erforderliches wert- volles Baumaterial belasten die Fundamente zusätzlich. Das ist weder bautechnisch noch ökologisch sinnvoll. Der naheliegende Vorschlag des für die Statik verantwortlichen Büros WSK Ingenieure sowie der für die Planung und Projektentwicklung zuständigen Taurecon lautete daher: Ausführung der Geschossdecken als Hohlkörperdecken.
Hohl kann mehr
Für die weitere Planung wurde mit dem Marktführer Cobiax schnell ein kompeten- ter Partner gefunden, der sich bereits seit Jahrzehnten intensiv mit der Technologie von Hohlkörperdecken beschäftigt. Das Unternehmen bietet unterschiedliche Systeme für Hohlkörperdecken an. Mit „Cobiax SL“ entschied man sich letztlich für ein besonders vielseitiges Modularsystem. Es eignet sich für die Deckendicke von 22 cm bis 56 cm, wobei Hohlraumhöhen von 10 cm bis 26 cm auf- gebaut werden. Hierfür werden auf der unteren Bewehrung Hohlkörpermodule fixiert. Diese bestehen aus je sechs Hohlkörpern, die über seitliche Stahlgitter in ihrer Lage zueinander fixiert sind. Abschließend wird die obere Bewehrung auf die Hohlkörpermodule aufgelegt und die Decke kann betoniert wer- den. Die in die STB-Decke eingebetteten Hohlkörper bewirken – je nach Decken- dicke – 53 l/m2 bis 135 l/m2 Einsparung an Beton, was zugleich einer Lastreduzierung von 132 kg/m2 bis 337 kg/m2 entspricht. Reduzierte Eigenlasten der Decken ergeben ein geringeres Biegemoment der Deckenkonstruktion, Bewehrungsstahl kann eingespart werden. Alle Geschosse in Summe ergeben deutlich reduzierte Fundamentlasten, womit eine zusätzliche Wirtschaftlichkeit über das Cobiax-System gegeben ist.
Von besonderem Wert für das QH Track erwies sich – neben dem modularen Aufbau von Cobiax SL – auch dessen mögliche Anlieferung in Einzelteilen für ein Zusammen- setzen vor Ort. Wie bei allen innerstädtischen Großbaustellen – in Berlin ganz besonders – sind Baustoffanlieferungen verkehrstechnisch schwierig und die Lagerflächen sehr begrenzt. Es war deshalb durchaus im Sinne von Peter Roy, dass nicht bereits fertig vor montierte Hohlkörperelemente geliefert wurden. Diese hätten einen deutlich erhöhten Lkw-Takt erfordert. Zugleich wäre eine Zwischenlagerung auf der Baustelle logistisch nur schwierig zu bewältigen. Angeliefert wurden nach Größe sortierte gestapelte Halbschalen und auf gesonderten Paletten die Fixierelemente in Form von Stahlgittern. Die Lagerhaltung gestaltete sich somit unproblematisch: je nach Deckendicke in ihrer Größe sortierte Halbschalen-Stapel, daneben die dazugehörigen Fixierelemente. Die hierdurch ermöglichte „größere Lagerhaltung“ entspannte die Problematik einer „just in time“-Lieferung deutlich. Es war immer genug auf Vorrat vorhanden.
Hohlkörpermodule anstatt Abstandsbewehrung
Der Aufbau der Bewehrung gestaltete sich nicht wesentlich anders als üblich. Ergänzend zu den Bewehrungsplänen wurden von Cobiax Verlegungspläne für die Hohlkörpermodule geliefert. Die Elemente wurden per Kran auf der Geschossdecke abgesetzt und per Hand exakt nach Plan verlegt. Das ließ sich aufgrund des geringen Gewichts leicht von zwei Personen bewerkstelligen, ebenso ein eventuell erforderliches Kürzen der Elemente. Hierzu mussten lediglich die vier Längsstäbe mit einer Mattenschere durchtrennt werden. Die unten überstehen- den Querstäbe der seitlichen Fixierelemente sorgen sofort nach dem Absetzen für eine Lagefixierung der Elemente. Vor dem Auf- legen der oberen Bewehrungslage werden sie zur endgültigen Lagefixierung noch mit Draht angebunden. Das alles dauert nicht länger als der Aufbau der sonst erforderlichen Abstandsbewehrung, ergibt insgesamt jedoch für die darauffolgende Betonage eine deutlich stabilere, gut begehbare Gitterstruktur.
Gearbeitet wird anders aber genauso schnell
Das Betonieren der Cobiax-Hohlkörperdecken erfolgt – anders als sonst üblich – in zwei Schritten. Zuerst wurde die untere Bewehrungslage einbetoniert, in einem zweiten Schritt die Hohlkörpermodule einschließlich der oberen Bewehrung. Dieser Ablauf muss sich erst ein wenig einspielen, wie Oberpolier Roy betonte: „Es gilt den Zeitpunkt zu treffen, an dem der Beton bereits so weit stoßfest angehärtet ist, dass er die untere Bewehrung mitsamt der angebundenen Hohlkörpermodulen so fest verankert, dass diese bei der zweiten Betonlage nicht mehr aufschwimmen können. Gleichzeitig muss er jedoch noch so frisch sein, dass er mit der zweiten Betonlage noch eine feste Verbindung ein- geht“. Ein wenig mehr Zeit beansprucht die Aufteilung in zwei Betonierschritte schon. Sobald jedoch der Takt stimmt, wird die annähernd gleiche Tagesleistung erreicht. Beim QH Track erwies sich ein Beton der Konsistenzklasse F4 als perfekt. Leicht fließend eingestellt verfüllte er alle Hohlräume zuverlässig. Zugleich wurden die Hohlkörpermodule gleichmäßig unterlaufen, ohne zu viel Auftrieb zu erzeugen. Falls bei der abschließenden Betonierung ein Hohlkörper dennoch leicht aufschwamm, wurde er einfach wieder in den Beton hineingedrückt.
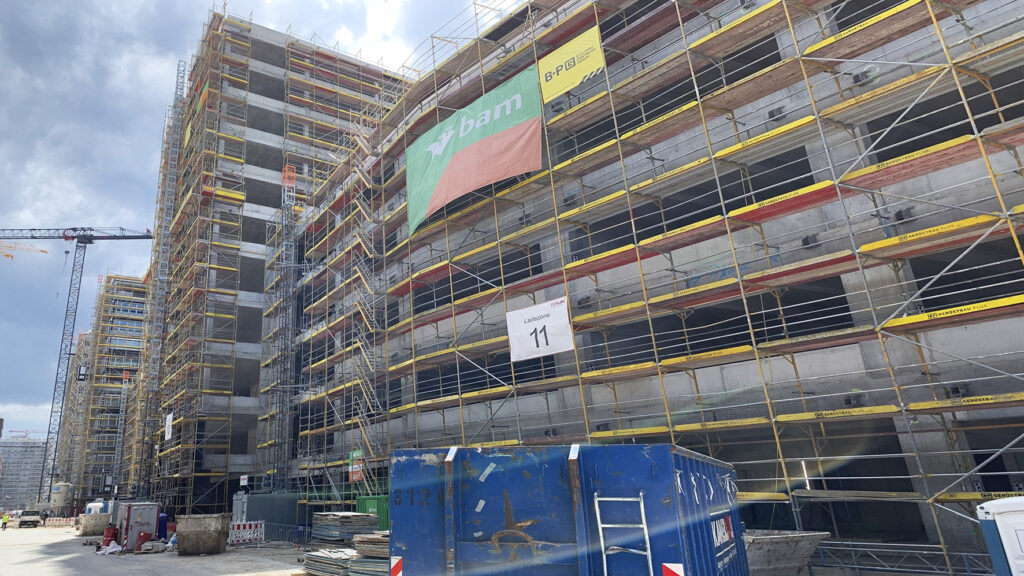
Verdichtet wurde wie sonst auch. Zwischen den Hohlkörpern ist ausreichend Platz für das Einführen der Rüttelflaschen. Kiesnester traten nicht häufiger auf als bei Standard-Stahlbetondecken. Generell wurde die obere Lage mit Rüttelplatten komplett nachverdichtet. Nicht zu vermeiden war, dass bei nachfolgenden Montagearbeiten Hohlkörper versehentlich angebohrt wurden und sich mit Regen- oder Tauwasser füllten. Das ist zwar statisch und auch bautechnisch kein Problem, aber: Wenn ein Hohlkörper angebohrt wird, kann dieser Schaden sofort erfasst oder möglichst gleich ausgebessert werden, das heißt: das Wasser wurde abgesaugt und das Loch abgedichtet.
Der Umwelt zuliebe Geld gespart
Auf den ersten Blick spart eine Cobiax- Decke natürlich viel Beton. Das sieht das Bauunternehmen sofort. Auch der Architekt erkennt die Vorteile einer schlankeren Konstruktion und Einsparungen bei der Fundamentierung des Gebäudes. Architektonisch und wirtschaftlich gesehen ist somit die Entscheidung für eine Hohlkörperdecke naheliegend. Baumaßnahmen jedoch rein nach wirtschaftlichen Erwägungen zu entscheiden, sind schon lange nicht mehr zeit- gemäß. Zunehmend in den Vordergrund gerückt sind die ökologischen Erwägungen. So sahen es die Verantwortlichen in Planung und Bauausführung auch beim QH Track in Berlin. Betoneinsparung und Lastreduzierung rückten also vorerst in den Hintergrund und die ökologischen Aspekte kamen auf den Prüfstand. Die Produktion von Beton und Stahl ist sehr energieintensiv und setzt somit große Mengen an CO frei. Durchschnittlich 35 % weniger Beton bedeuten rd. 0,011 t bis 0,028 t Einsparung an CO2 pro Quadratmeter. Bei 100000m2 Geschoss-decke – so wie beim QH Track – mit einer durchschnittlichen Dicke von 32 cm werden rd. 2 000 t CO2 eingespart. Und dies nicht nur fernab in einem Industriegebiet, sondern auch direkt vor Ort, mitten in Berlin. Nicht umsonst weist die Deutsche Gesellschaft für nachhaltiges Bauen ausdrücklich darauf hin, wie wichtig geringer Transportaufwand und kurze Wege für ein nachhaltiges Bauen sind.
Die Hohlkörper werden zu 100% aus Recycling-Kunststoff hergestellt und tragen somit maßgeblich zur Ressourcenschonung bei. Mit dem Großbauprojekt Quartier Heidestrasse zeigen alle Projektverantwortlichen, wie einfach eine Ökobilanz verbessert werden kann und zugleich, dass Umweltschutz nicht unbedingt Geld kostet.